C2 PROJECT
C2 Photo Album
album:Autumn 2019
September and October working parties
On the Driver's side cylinder we wanted to bore out as little material as possible, so it was imperative to get it perfectly aligned on the borer. This shows part of the setup process.
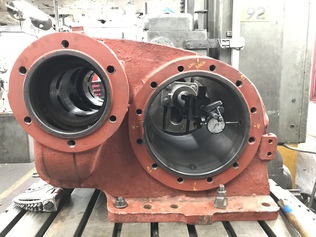
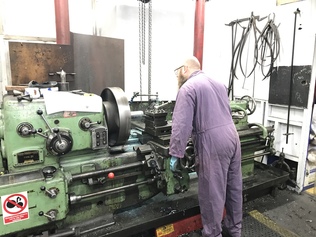
Dave 2 at work machining the new reverser weighshaft.
Dave 1 and Colin check the alignment of the cylinder on the borer. This is a large machine and it's often easier to work with 2 people.
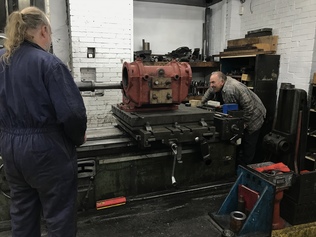
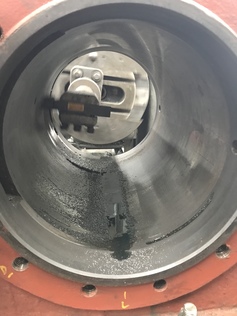
Cylinder boring in progress
The completed bore of the driver's side cylinder.
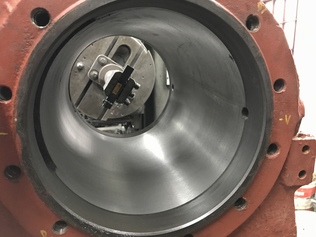
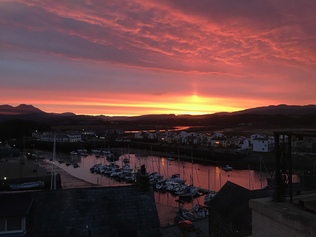
Sunrise over Porthmadog, just before the Victorian Weekend. This autumn has seen some extremes of weather and there have been many other days when we have been very glad to be working indoors.
Victorian weekend: Blanche and Linda pass a freight train hauled by Taliesin, at the remote passing loop at Rhiw Goch. C2 Project members were fully employed on the locos and/or as wagon brakesmen over the weekend: on this occasion Sam was driving Blanche while Paul was driving Taliesin.
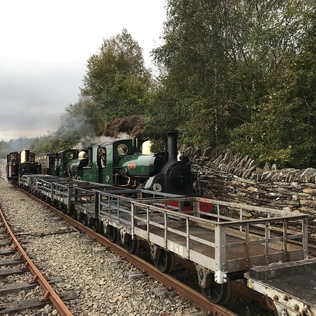
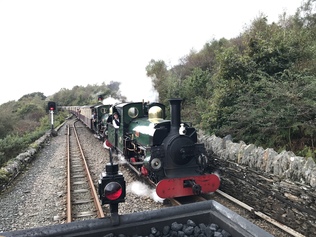
A brake hanger bracket, with the chilled spigot pressed into the bracket.
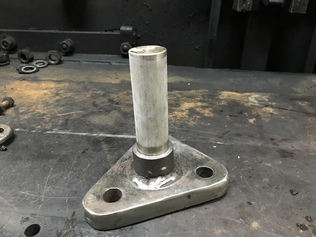
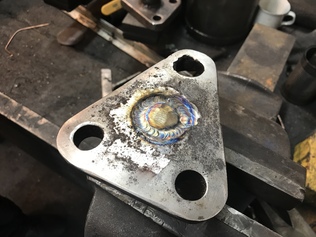
Robco did some very neat TIG welding on a couple of these to ensure the spigot was reliably secured.
The sun lights up the newly machined cylinder bore.
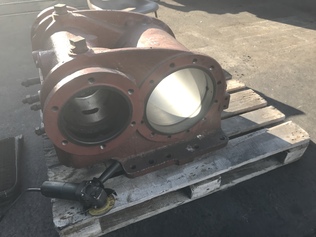
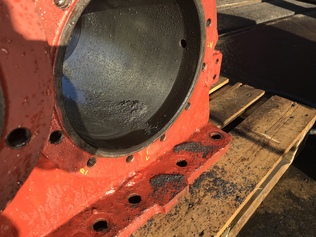
Steam-cleaning the insides of the cylinder ports and passages was a very effective way of removing the accumulated swarf.
After steam-cleaning, Alan uses an air lance to dry the cylinders and remove any remaining loose particles.
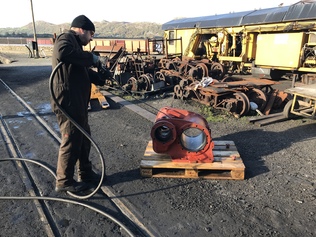
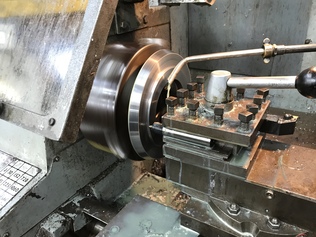
Andrew machined some more coupling rod bearing covers; these are progressing well.
...and posted the pallet through the doorway. It's a tight fit!
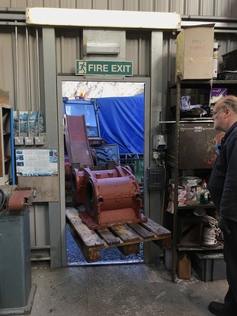

Delivering the cylinders back into our shed was tricky, but Matt very carefully manouevred the Manitou past the obstructions...
Erle has nearly finished two of the lubricators. Here is one of them.
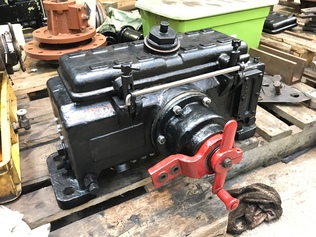
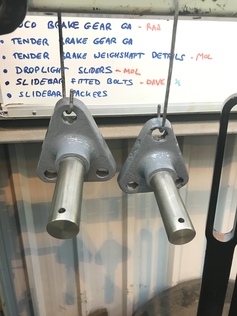
Brake hanger brackets now complete and in primer.
Tender and loco crash beams. All these need now is a coat of special paint on the footsteps, and they will be ready to fit to the bufferbeams.

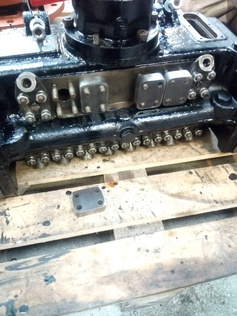
The underside of one of the lubricators showing the refurbished pumps and new blanking plates fitted. By making the blanks to the same thickness as the pump bodies, standard studs and nuts can be used.
The lubricators are steam-heated, a necessity with thick cylinder oil in the -40C temperatures of north-eastern China. It won't be so cold in Wales, but having warm oil makes it easier to pump so we are keeping the steam heating feature. This has required some new steam pipes and end fittings which Erle has made.
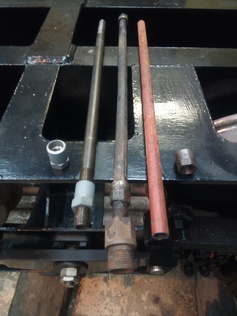
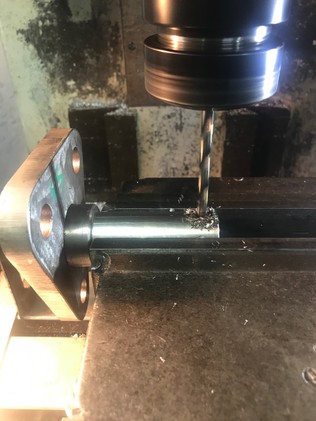
Drilling the holes for the retaining split pins was most accurately done in the Bridgeport mill by Alan and Dave 2.
Paul steam-cleans the cylinders.
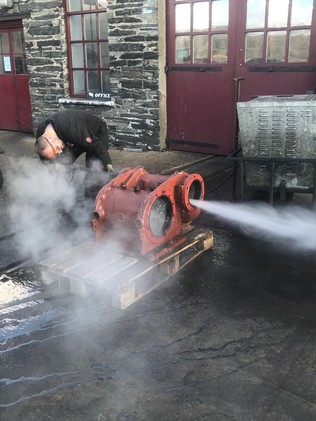
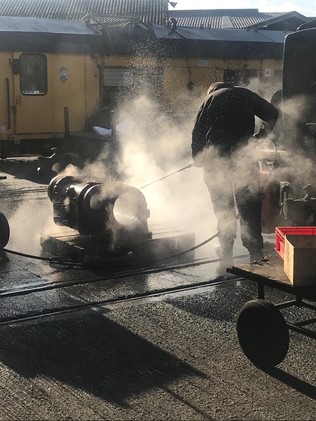
Hopefully it won't be too many years before these cylinders are filled with steam from our new boiler!
Paul used an angle grinder to remove some casting flash on the cylinders, prior to cleaning them.
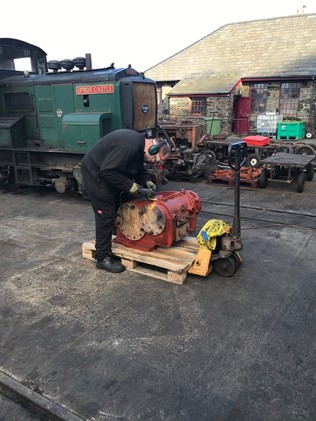
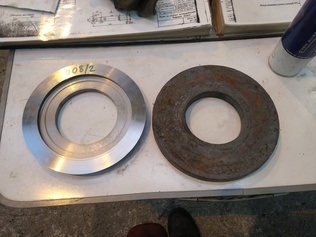
Before and after pictures of turning a ring of steel into a coupling rod roller bearing cover - Andrew Nelms 28/10/2019
Before and after pictures of turning a ring of steel into a coupling rod roller bearing cover - Andrew Nelms 28/10/2019
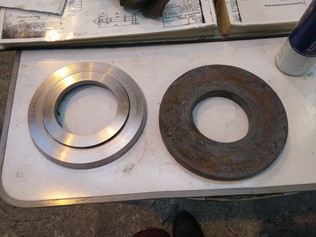